Heavy industrial machinery which have reciprocating, impact, rotating masses and other machinery generating dynamic loads like crushers, hammers, punch presses often need a machinery support system that can resist dynamic forces and the resulting vibrations. It may be elastomeric isolators, large inertial mass, steel coil springs and viscous fluid dampers or a varied combination of these.
Forging Hammers, Punching machines, Metal Forming Presses and other types of shock producing machines generate powerful short-period impact loads, characterized as shock pulses. Only a part of the shock energy is utilized in the intended hammering, punching, pressing, shaping operations and the rest is dissipated in the foundation causing intense vibration.
The pre-impact kinetic energy of the ram converts to post-impact kinetic energy of the entire machine, forging hammer etc. making it oscillate.
Shocks from hammer foundations transmit to the soil and surroundings causing horizontal soil vibrations that may induce resonant building oscillations while ground vibrations that are transformed in series of harmonic waves with the predominant frequency equal to the frequency of vertical vibrations of the source.
This, oscillation has to be arrested or sufficiently decayed before the next impact.

These excessive-machine-generated-vibrations, are detrimental to:
- The proper operation of the machinery installations, technological systems, and other workshop components.
- Cause damage / enhance maintenance cost of the building and the structures, dynamic settlements of column footings, where the machinery is installed.
- Generate waves, high amplitude impact shock pulses and noises that transmit to the environment, affecting the foundations of sensitive installations and equipment, besides causing discomfort / fatigue for the workshop personnel.
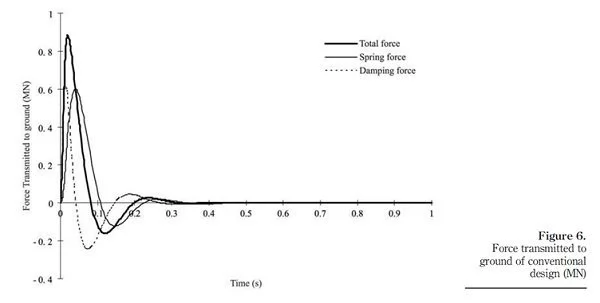
In India, operation of large impact machines (like Mechanical presses, Forging Hammers, Punch presses , etc.) with very high dynamic loads causing heavy shocks transmission to the foundation can cause alignment problems , neighbour complaints and prohibit proper operation of nearby equipment / machinery. Therefore, to limit the transmissibility of shock forces to the foundation we need to mitigate the vibration amplitudes and the forces transmitted to the soil.
Several Methods practiced over years for Hammer Foundation Vibration Isolation are:
1.Stabilisation of Soil:
Stabilization of soil increases the rigidity of the base, thereby increases the natural frequencies of the foundation resting directly on soil through chemical, geosynthetics or cement stabilization, in consultation with geo-physicist and architectural engineers.
2. Structural Measures:
Increasing base area or mass of foundation: Depending upon the frequency ratio, either increasing the base area or increasing the mass of the foundation, whichever is considered appropriate, may be adopted in consultation with the structural and civil engineers. But, the level of vibration isolation achieved is never satisfactory or adequate for any practical purposes.
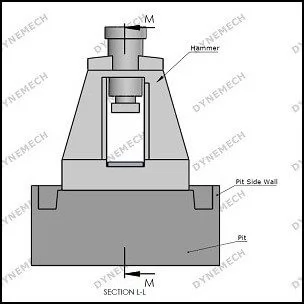
Interposing isolating media: Isolating media such as Dynemech Vibration Insulation tiles , Dynemech Viscous Dampers are introduced between the machine and the foundation to effectively increase the amplitude of the motion and decrease the natural frequency of the systems to reduce the vibration and shock transmission.
Dynemech Foundation Installation Configurations for Forging Hammers
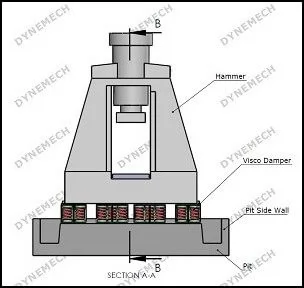
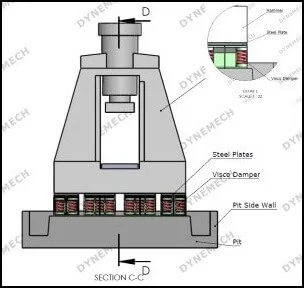
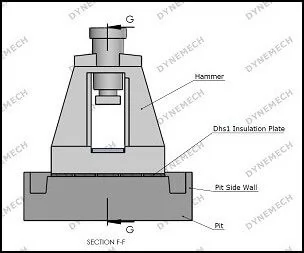
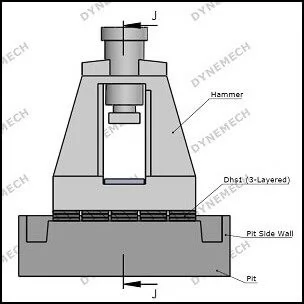
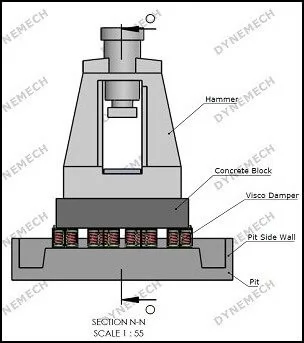
Weight of the hammer, dynamic forces, generated by the hammer, base area of the anvil, soil bearing capacity of the site and type of soil (to be determined by a structural engineer), water table depth at the site (to be determined by a structural engineer), the stiffness of the isolator and damping ratios of the vibration isolators, Ram weight, Drop Height , no. of strokes per minute , and support area of soil are taken as design variables of vibration dampers and foundations for high dynamic vibrating equipment.
Research on “Influence of foundation types on kinematics and dynamics of forging hammers” clearly roots for the effectiveness of mounting of the hammer on a foundation (type b) consisting of: a sub-anvil pad, reinforced concrete block, vibro-isolator and reinforced concrete foundation trough. But the economics and time frame of hammer installation, do not always permit so.

The traditional solutions of elastic foundations to install forging hammers, required large inertial mass made of concrete under the hammer. But, experience and research have proven how less desirable it is as it is prone to cracks and very poor vibration damping.
Dynemech Elastomeric Tiles
Elastomer based shock absorber pads are superior for forging hammers installation as they provide faster and easier installation and quicker assembly of hammer to meet manufacturing pressures. But, Elastomeric material provide lower vibration isolation characteristics, as compared to Vibration Isolators with springs and viscous dampers.

Restrictions in available area for the machine’s foundation inertial mass slab, besides easier and quicker installation of hammer, and guidelines for vibration control also necessitates the use of Viscous Damped Spring Vibration Isolators.
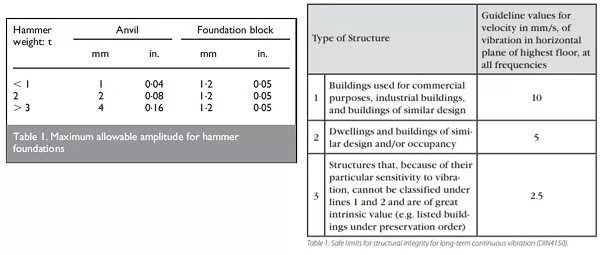
How does the Dynemech Viscous damped Spring Vibration Isolation Systems for Forging Hammer?
After the impact caused by the collision of ram and the anvil, the forging hammer moves down on the support structure and starts oscillating. The kinetic energy generated is passed on to the supporting structure after the intended forging / metal-forming operation is performed. Dynemech Shock Isolators mitigate the vibration transmission through two mechanisms:
1.Shock is isolated by the motion of the isolator and internal viscous damping of the Dynemech vibration isolators. The force transmitted to the base and the motion of the ground/foundation are both reduced considerably.
2.Dynemech shock isolators reduce the severity of the shock experienced by the equipment by increasing the duration of shock to be transferred to the ground/foundation and provides considerable reduction of its reversal back to the machines.
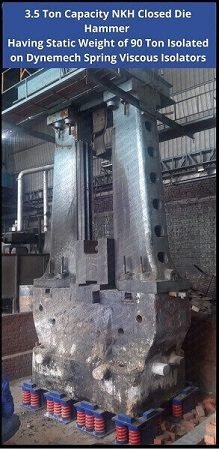
Characteristics of Dynemech Spring Isolators:
- Dynemech use spring isolators having much lower stiffness that the supporting structures, lowering the natural frequency of the forging hammer-foundation system.
- Viscous damping is provided to bring oscillating hammer to rest before the next blow.
Since, the vertical movement of metal-forgings depends on, the mass of the anvil and rigid systems, ( changes in the system of hammers decreases when the mass anvil increases and movement increases with less rigid systems of lower natural frequency), an appropriate selection of the viscous damped spring isolators is needed such that the weight of anvil would maintain the natural frequency and characteristics of isolation performance. Also, after serious, accurate calculations, performance must be accurately gauged so that the endurance limit is never exceeded, and ideal isolation efficiency is achieved.
Moreover, the natural frequency of the vibrating forging hammer-foundation system , which is defined by the stiffness of the spring vibration dampers or elastomeric vibration dampers and the supported mass should be designed in such a way that it differs significantly from the resonant frequency of the solid concrete foundation.
Viscous damped spring isolators can considerably reduce the size and depth of foundation, cost of designing hammer foundation and improve the performance of the forging hammer foundation.
Dynemech Spring Viscous Dampers for Forging Hammers
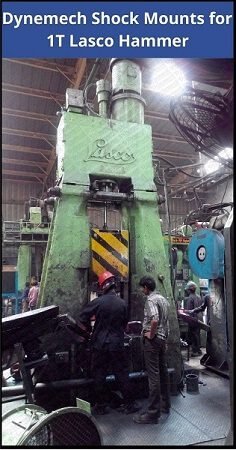
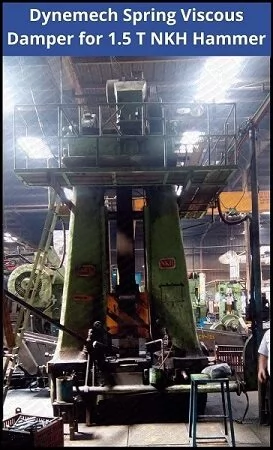
Benefits of Dynemech Spring Viscous Dampers
- High Vibration Control performance upto 80% .
- High life and durability of Dynemech Viscous Damper Mounts
- High efficiency Low deflection Springs with Viscous Damping .
- Heavy duty, rugged Body construction of Dynemech Viscous Dampers.
- Extended machine and tool life.
- Reduced building and machinery maintenance.
- No compromise on Forging and Forming efficiencies and hammer ram force.
- Reduce foundation depth size, effectively reducing foundation size – initial lowered cost of Hammer foundation and easy to relocate the Hammer, if need be.
- Vibration mitigation controls operator fatigue / discomfort and improves working environment.
- Aids quicker hammer installation with decreased foundation building costs.
- Protection from pollution norms and Neighbourhood vibration transmission complaint.
- Reduce machine maintenance and high die life.
- Assists in better plant layout with convenient operation of allied machinery and equipment.
- Side stops in shock isolator design prevents machine slipping.
Vibration Insulation system Repair Services:
Besides, designing and manufacturing Vibration Isolation Systems for Forging Hammers, we also assist with repair and servicing of forging hammers vibration isolation systems of any make and design.
Dynemech engineers work on the structural integrity of the isolator body, dimensional tolerances of the springs and viscosity composition of the damping fluid to get the system in perfect working condition again.